Gymnastic Polymers
by Alexander Hili
Robot Maps, Robot Moves, Robot Avoids
Robotics is a cornerstone for this century’s innovations. From robot nurses to your own personal assistant, most robots need to know: ‘where is it?’ ‘Where should it go?’ And ‘how to get there?’ Without answers to these questions a robot cannot do much.Continue reading
Wear Resistant Aluminium
Aluminium alloys have a low density and are easy to make. These qualities make them popular in the transport industry which can range from cars to planes. A low density makes them perfect to reduce weight in large metal structures. Unfortunately due to poor wear resistance, aluminium alloys can deteriorate quickly which severely limits their applications.
Dr Clayton D’Amato (supervised by Dr John C. Betts and Dr Joseph Buhagiar) modified the surface of an aluminium alloy (called A356) to overcome such limitations by improving wear resistance. D’Amato used a high power industrial CO2 laser to rapidly melt specific regions of the alloy’s surface. He simultaneously introduced additional alloying elements in the melt pool, which mix with the base metal to form new compounds that reinforce the soft aluminium surface. In this way, he formed a strong composite modified surface. Additional experimentation allowed D’Amato to reduce the loss of material due to wear by about 20 times. He optimised the conditions needed to laser process the surface of the aluminium in a uniform and repeatable manner. Adding nickel increased surface hardness 7-fold due to formation of aluminium-nickel compounds. Additional strength was achieved by adding hard ceramics to this aluminium-nickel structure. D’Amato created fine titanium carbide (TiC) particles in a matrix structure (pictured) by alloying a mixture of nickel, titanium and carbon (Ni-Ti-C). Aluminium treated in this way was much stronger.
The exact hardness was related to the mix of alloying elements in the modified surfaces. Hardness improved wear resistance, with large improvements in both surfaces alloyed with nickel and Ni-Ti-C. They lost 20 times less material than normal aluminium preventing severe damage.
Using a high powered laser allows improved wear resistance just where needed. This saves costs and increases versatility. The above technique could be used to manufacture aircraft pump parts, fittings and control parts, and in automotive water-cooled cylinder blocks.
This research was performed as part of a Ph.D. in Engineering within the Faculty of Engineering at the University of Malta. It was partially funded by the Strategic Educational Pathways Scholarship (Malta). This Scholarship is part-financed by the European Union — European Social Fund (ESF) under Operational Programme II — Cohesion Policy 2007–2013, “Empowering People for More Jobs and a Better Quality Of Life”. The laser processing equipment used in this project was financed by the 4th Italian protocol whilst the characterisation equipment was financed by the European Regional Fund (ERDF) through the project “Developing an Interdisciplinary Material Testing and Rapid Prototyping R&D Facility (Ref. no. 012)”.
An Intelligent Pill
Doctors regularly need to use endoscopes to take a peek inside patients and see what is wrong. Their current tools are pretty uncomfortable. Biomedical engineer Ing. Carl Azzopardi writes about a new technology that would involve just swallowing a capsule.
Michael* lay anxiously in his bed, looking up at his hospital room ceiling. ‘Any minute now’, he thought, as he nervously awaited his parents and doctor to return. Michael had been suffering from abdominal pain and cramps for quite some time. The doctors could not figure it out through simple examinations. He could not take it any more. His parents had taken him to a gut specialist, a gastroenterologist, who after asking a few questions, had simply suggested an ‘endoscopy’ to examine what is wrong. Being new to this, Michael had immediately gone home to look it up. The search results did not thrill him.
The word ‘endoscope’ derives from the Greek words ‘endo’, inside, and ‘scope’, to view. Simply put, looking inside our body using instruments called endoscopes. In 1804, Phillip Bozzini created the first such device. The Lichtleiter, or light conductor, used hollow tubes to reflect light from a candle (or sunlight) onto bodily openings — rudimentary.
Modern endoscopes are light years ahead. Constructed out of sleek, black polyurethane elastometers, they are made up of a flexible ‘tube’ with a camera at the tip. The tubes are flexible to let them wind through our internal piping, optical fibers shine light inside our bodies, and since the instrument is hollow it allows forceps or other instruments to work during the procedure. Two of the more common types of flexible endoscopes used nowadays are called gastroscopes and colonoscopes. These are used to examine your stomach and colon. As expected, they are inserted through your mouth or rectum.
Michael was not comforted by such advancements. He was not enticed by the idea of having a flexible tube passed through his mouth or colon. The door suddenly opened. Michael jerked his head towards the entrance to see his smiling parents enter. Accompanying them was his doctor holding a small capsule. As he handed it over to Michael, he explained what he was about to give him.
Enter capsule endoscopy. Invented in 2000 by an Israeli company, the procedure is simple. The patient just needs to swallow a small capsule. That is it. The patient can go home, the capsule does all the work automatically.
The capsule is equipped with a miniature camera, a battery, and some LEDs. It starts to travel through the patient’s gut. While on its journey it snaps around four to thirty-five images every second. Then it transmits these wirelessly to a receiver strapped around the patient’s waist. Eventually the patient passes out the capsule and on his or her next visit to the hospital, the doctor can download all the images saved on the receiver.
The capsule sounds like simplicity itself. No black tubes going down patients’ internal organs, no anxiety. Unfortunately, the capsule is not perfect.
“The patient just needs to swallow a small capsule. That is it. The patient can go home, the capsule does all the work automatically”
First of all, capsule endoscopy cannot replace flexible endoscopes. The doctors can only use the capsules to diagnose a patient. They can see the pictures and figure out what is wrong, but the capsule has no forceps that allow samples to be taken for analysis in a lab. Flexible endoscopes can also have cauterising probes passed through their hollow channels, which can use heat to burn off dangerous growths. The capsule has no such means. The above features make gastroscopies and colonoscopies the ‘gold standard’ for examining the gut. One glaring limitation remains: flexible endoscopes cannot reach the small intestine, which lies squarely in the middle between the stomach and colon. Capsule endoscopy can examine this part of the digestive tract.
A second issue with capsules is that they cannot be driven around. Capsules have no motors. They tend to go along for the ride with your own bodily movements. The capsule could be pointing in the wrong direction and miss a cancerous growth. So, the next generation of capsules are equipped with two cameras. This minimises the problem but does not solve it completely.
The physical size of the pill makes these limitations hard to overcome. Engineers are finding it tricky to include mechanisms for sampling, treatment, or motion control. On the other hand, solutions to a third problem do exist. This difficulty relates to too much information. The capsule captures around 432,000 images over the 8 hours it snaps away. The doctor then needs to go through nearly all of these images to spot the problematic few. A daunting task that uses up a lot of time, increasing costs, and makes it easier to miss signs of disease.
A smart solution lies in looking at image content. Not all images are useful. A large majority are snapshots of the stomach uselessly churning away, or else of the colon, far down from the site of interest. Doctors usually use capsule endoscopy to check out the small intestine. Medical imaging techniques come in handy at this point to distinguish between the different organs. Over the last year, the Centre for Biomedical Cybernetics (University of Malta) has carried out collaborative research with Cardiff University and Saint James Hospital to develop software which gives doctors just what they need.
Following some discussions between these clinicians and engineers they quickly realised that images of the stomach and large intestine were mostly useless for capsule endoscopes.
Identifying the boundaries of the small intestines and extracting just these images would simplify and speed up screening. The doctor would just look at these images, discarding the rest.
Engineers Carl Azzopardi, Kenneth Camilleri, and Yulia Hicks developed a computer algorithm that could first and foremost tell the difference between digestive organs. An algorithm is a bit of code that performs a specific task, like calculating employees’ paychecks. In this case, the custom program developed uses image-processing techniques to examine certain features of each image, such as colour and texture, and then uses these to determine which organ the capsule is in.
Take colours for instance. The stomach has a largely pinkish hue, the small intestine leans towards yellowish tones, while the colon (unsurprisingly perhaps) changes into a murky green. Such differences can be used to classify the different organs. Additionally, to quickly sort through thousands of images, the images need to be compacted. A specific histogram is used to amplify differences in colour and compress the information. These procedures make it easier and quicker for algorithm image processing.
Texture is another unique organ quality. The small intestine is covered with small finger-like projections called villi. The projections increase the surface area of the organ, improving nutrient absorption into the blood stream. These villi give a particular ‘velvet-like’ texture to the images, and this texture can be singled out using a technique called Local Binary Patterns. This works by comparing each pixel’s intensity to its neighbours’, to determine whether these are larger or smaller in value than its own. For each pixel, a final number is then worked out which gauges whether an edge is present or not (see image).
Classification is the last and most important step in the whole process. At this point the software needs to decide if an image is part of the stomach, small intestine, or large intestine. To help automatically identify images, the program is trained to link the factors described above with the different organ types by being shown a small subset of images. This data is known as the training set. Once trained, the software can then automatically classify new images from different patients on its own. The software developed by the biomedical engineers was tested first by classification based just on colours or texture, then testing both features together. Factoring both in gave the best results.
“The software is still at the research stage. That research needs to be turned into a software package for a hospital’s day-to-day examinations”
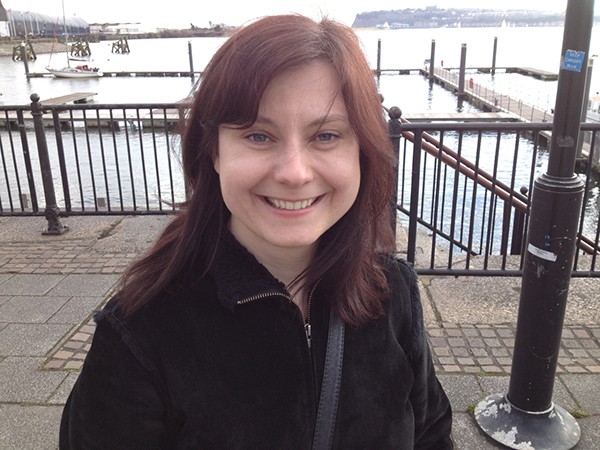
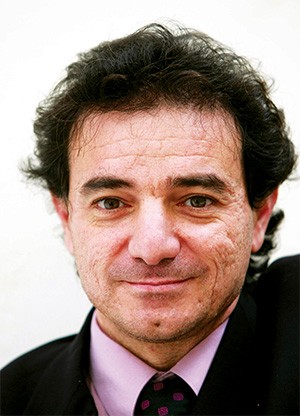
After the images have been labeled, the algorithm can draw the boundaries between digestive organs. With the boundaries in place, the specialist can focus on the small intestine. At the press of a button countless hours and cash are saved.
The software is still at the research stage. That research needs to eventually be turned into a software package for a hospital’s day-to-day examinations. In the future, the algorithm could possibly be inserted directly onto the capsule. An intelligent capsule would be born creating a recording process capable of adapting to the needs of the doctor. It would show them just what they want to see.
Ideally the doctor would have it even easier with the software highlighting diseased areas automatically. The researchers at the University of Malta want to start automatically detecting abnormal conditions and pathologies within the digestive tract. For the specialist, it cannot get better than this.
The result? A shorter and more efficient screening process that could turn capsule endoscopy into an easily accessible and routine examination. Shorter specialist screening times would bring down costs in the private sector and lessen the burden on public health systems. Michael would not need to worry any longer; he’d just pop a pill.
* Michael is a fictitious character
[ct_divider]
The author thanks Prof. Thomas Attard and Joe Garzia. The research work is funded by the Strategic Educational Pathways Scholarship (Malta). The scholarship is part-financed by the European Union — European Social Fund (ESF) under Operational Programme II — Cohesion Policy 2007–2013, ‘Empowering People for More Jobs and a Better Quality of Life’
Netherlands: a land of bikes, clogs, and research
My journey started in 2006, when I started my bachelor in Mechanical Engineering (University of Malta). My passion lay in Materials Engineering, so I focused my undergraduate thesis in this area. I studied ways of improving the corrosion resistance properties of Nitinol, an alloy of Nickel and Titanium. This material is used in many biomedical applications. I built an environment similar to the human body to test the material’s corrosion properties.
After graduating in 2010, I took an M.Sc. in biomedical engineering and specialised in biomaterials (Delft University of Technology, Netherlands). Over this two-year programme as part of my technical internship, I worked at the Orthopaedics Research Department of the Erasmus Medical Centre (Rotterdam). I worked with two other Ph.D. students researching titanium scaffolds for bone defects.
Following my internship, I moved back to Delft and performed another research project again on the alloy Nitinol. We were using it to improve heart stents, tubes used to prop open blood vessels when they are clogged. I created a layer of a ceramic, porous Titanium dioxide, on the surface of Nitinol and then filled the pores with a novel drug that prevents the blockage of blood vessels. Heart stents sometimes fail by getting clogged, the slow release of the drug, which we monitored, would help prevent blockages hence heart attacks at a later date.
But my time in Delft was not yet over. I remained at TU Delft to take up a two-year research position. This time I am researching how natural polymers can be used to make artificial cartilage tissue for patients who need it replaced — a challenging project since I am learning how to set up a new lab for a new subject.
Cuschieri was awarded a STEPS scholarship for her Masters studies, which is part-financed by the EU’s European Social Fund under Operational Programme II — Cohesion Policy 2007–2013.
Should Malta Be The Next China?
After repeatedly visiting Asia, I totally disagree with comments occasionally made that China’s industrial success is wholly attributed to its ability to replicate low quality versions of branded products at rock-bottom prices. In China there are many good examples of good quality products and brands being produced such as Audi, Airbus, and Armani. Based on these facts, what Maltese industry and policy makers should focus on is making our industry more competitive by improving the current situation and analyzing products being developed elsewhere.
The Maltese industry is not really dying. Our industry has indeed changed, for example from textiles to pharmaceuticals. Overall, the number of employees has declined. However, this is either due to industry becoming more efficient hence able to produce more with less, or due to the way statistical data is being collected.
Malta’s industrial sector can become more competitive. However, what does it mean to ‘be competitive’? Goods should be produced with shorter delivery periods, better costs and quality compared to competitors. Since we lack raw materials cost is very challenging to compete on. On the other hand, improving quality provides much more opportunity. Quality can be improved by increasing the external quality of the products manufactured, the product’s functionality, the interactions that take place with clients during product development, the quality of support and after sales services, management of operations, and how operators work. Core to adopting this quality-based approach is the need to focus on shifting from just manufacturing products to designing and manufacturing products in Malta.
“Goods should be produced with shorter delivery periods, better costs, and quality compared to competitors”
To design their own products, Maltese manufacturing firms need to set up an internal Research & Development unit. At the same time, industry needs support through government policies and incentives. In their publication ‘Vision 2015’ American consultants clearly specify product design as an enabler to higher value added manufacturing. The Malta Chamber of Commerce, Enterprise & Industry has also recommended starting a Malta Business Research & Innovation Body. These recommendations need urgent implementation to shift Malta’s manufacturing industry towards becoming ‘design driven’.
The UoM’s Faculty of Engineering has been actively contributing towards a design driven approach. Our undergraduate engineers are purposely trained in this design-centric approach. Additionally, some final year student projects focusing on design are sponsored by industry: an excellent win-win mechanism. A number of both mechanical and electrical engineers have also benefited through an evening M.Sc. in Integrated Product Development. The Faculty also collaborates with industry through MCST funded Research & Innovation projects. More financial support to University would help every academic active in research to regularly receive decent research funds.
Considering the above, Malta does not and should not aim to be the next China. On the other hand, Malta should nurture its unique strengths such as a highly educated, flexible English-speaking workforce. We should aim to address weaknesses related to Malta’s manufacturing sector. This requires short-term and long-term commitments from our policy makers. Business leaders can also proactively embrace change by aiming to offer quality and innovative solutions, rather than aiming for higher production rates of existing products. The Maltese industry should support continuous training and collaborate on research activities with University. The UoM can help them become more innovative. Like Airbus, Armani, and Audi, Maltese business leaders should exploit, rather than fear, Asian industry. Some Malta based entities, such as Toly Products Ltd, are already going down these routes and are reaping the rewards of growth during a recession. Clearly others should aim to do the same to keep Malta competitive.
Have there been any studies to modify the domestic refrigerator into part fridge and part air conditioning unit?
Asked by Tony Bugeja
Racing into the Future
Way back in 2007, a dedicated group of six people put together a formula-style race car in just six months to compete in a prestigious international competition called FSAE. Since then no other team has participated. Students were always interested to build a racing car but found it too hard to actually carry out — the underlying logistics were simply too much.
In December 2012, a group of motivated university students founded the University of Malta Racing (UoMR) team. Their mission statement: ‘To encourage and facilitate students of the University of Malta to unite together as a team in the planning, design and construction of a Formula-style race car and to participate in the Formula SAE, or similar competitions.” They were brought together by a love of cars, engines, speed and a competitive spirit.
The 2007 team placed 17th out of 20 teams. The new team has stiff competition and huge challenges to overcome for the upcoming competition in July 2014. Foreign universities compete every year and build a database of knowledge and experience which students use to continue improving their cars. For the UoM to compete eff
ectively with top-class international universities, there must be a strong framework which supports and encourages students from every faculty, especially the Faculty of Engineering. To overcome this challenge the team extensively researched the parts, materials needed and procedure to build a competitive vehicle. The PR and Finance team of the UoMR also drew up a sponsorship proposal, which was used to attract sponsors and collaborators. Without them the project would not be possible.
The team is currently working on the car’s design. At the same time they are fabricating some parts and structures inside their workshop at University. They are looking for financial or in kind assistance from driving enthusiasts and organisations. •
For more information on UoMR and contact details visit: uomracing.com. The University of Malta’s research trust, RIDT, fully supports the UoM racing team initiative. The trust aims to sustain and grow the UoM’s research activity. Please consider making a contribution at www.ridt.eu